Sufficient Thickness of the Screed
The thickness of the screed that is installed will depend on the type of screed, type of flooring, the type of traffic and the intensity of the traffic acting.
Mechanical Resistance of the Screed
The screed must gain sufficient thickness with mechanical strength in order to safely support the floor structure coming over it. The mechanical strength of a screed that is installed for flooring in the case of domestic application will have a minimum value of 20MPa. This value can be 30MPa in the case of Industrial floor installation.
Compactness of the Screed
The screed must possess compactness throughout the thickness of the same. Any occurrence of crumble areas or inconsistency resembles the lack of mechanical resistance. This will result in the detachment or the breakage of the flooring. These areas have to be properly assessed and repaired based on the extent of the defect.
Properly cured and Dimensionally Stable Screeds
Adequate time has to be given for the installed screed for proper curing and completion of most of the shrinkage issues. Only after this provision, the installation of the floor has to be conducted. The curing cycle of the screed will make them prone to hygrometric shrinkage. This is as a result of evaporation of water and the drying off. This effect will cause curling or cracking as shown in figure-2 and figure-3.
|
Fig.1. Deformation Caused in Flooring due to "Curling" |
|
Fig.2. Cracks formed in Floors |
The cracks that are formed after the installation of flooring system will result in the detachment or the damage of the floor, as shown in figure-4.
|
Fig.3. Serious Damage Caused due to Curling after the Installation of Floors
|
Note: The time for curing for traditional mix of sand and cement is around 7 -10 days per centimeter of thickness for a good condition of weather. The screed that is made from the cementitious material can be longer say more than 1 month. The use of special admixture or special binders will help in reducing the curing times to a large extent.
Crack Free Screeds
A number of reasons can result in cracks in screeds. These reasons will include hygrometric shrinkage, use of fine aggregates in a large amount, a large amount of cement, too much water in the mix. All the cracks seen in the screed must be sealed monolithically before the application of the floor over it. The epoxy resins like EPORIP or EPOJET can be used to seal the cracks. The presence of hairline cracks will ask for the laying of an anti-fracture membrane. This can be MAPETEX.
Clean and Dry
The screed surface has to be clean free from dirt, dust and detached areas. Rubbles or any other material have to be removed and cleaned from the surface before the installation of the floors. These materials will hinder the adhesion between the screed and the floor.
|
Fig.4. Detached Floor System From Screed due to Improper Adhesion |
The residual humidity of the screed has to be checked so that it conforms to the maximum level for the type of screed system that is installed. This is because the flooring is highly sensitive to the humidity.
|
Fig.5: Carbide Hygrometer to Measure the Relative Humidity in Screeds |
For anhydrite screeds, the value of relative humidity must be less than 0.5%, irrespective of the type of floor cover installed. For screeds of the cementitious type, the value of R.H. is lesser than 2% for wooden floors and for PVC material floor types it is less than 2.5 to 3%.
The smoothness of the Screed
The grade of finish of the screed is chosen based on the type of flooring that is installed. This will decide the level of roughness or the level of smoothness. The rough surface helps the floor to dry out easily and promotes good adhesion properties with the floor system. In the case of installation of resilient flooring there comes the need for a smooth finish.
Flatness of the Screed
Laying a straightedge at least 2m long in all directions on the screed surface will let us measure the flatness of the screed. The max: tolerance with this particular straight edge can be 2mm. If the flatness is not intolerant, the surface must be leveled properly before installation of the flooring system.
|
Fig.6: Method that is used to Check the Flatness of the Flooring |
Composition of Screed
Conventional screed is made from cement and sharp sand. To get a thicker layer, coarse aggregates can be used for industrial purposes. Compared to screed, concrete is more coarser and stronger, given that they both form a type of cement mixture.
Based on the type of mixture, screeds can be:
1. Dry Screed
A dry screed is a pre-mixed material typically composed of sand and cement, which is applied in a dry form and doesn't require water during installation. It is commonly used as a leveling and smoothing layer for various floor finishes such as tiles, wood, or laminate.
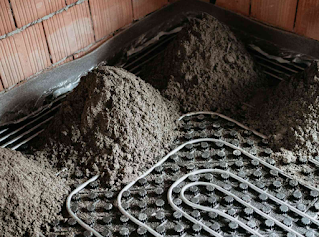
Dry screed is known for its rapid drying time, allowing for quicker installation of subsequent flooring materials.
2. Flowing or Liquid Screed
Flowing screed, on the other hand, is a self-leveling compound that includes gypsum or calcium sulfate binders. This type of screed is mixed with water and poured onto the floor, allowing it to flow and self-level. A flowing screed is ideal for large areas, providing a smooth and even surface. It is commonly used in projects where a high-quality finish and quick installation are crucial, such as in residential and commercial buildings.
Types of Screed in Construction
The three main types of screed are bonded, unbonded, and floated screeds. Let's discuss one by one.
1. Bonded Screed
Bonded screeds are types of screeds that are bonded to the given slab or substrate below by means of a bonding agent. It is typically used for projects where heavy loading is common like driveways, carways, or in underfloor heating system construction.
 |
Bonded Screed |
The bonded screed fails when the bond between the screed and the substrate fails. This is more likely to happen when the thickness of thickness is high. Hence, the thickness of bonded screed is limited below 50mm i.e. between 25 to 40 mm.
2. Unbonded Screed
The screed layer that is intentionally unbonded from the below substrate layer by means of a membrane is called an unbonded screed. A PVC/damp-proof membrane is used to separate the layers, especially in areas where damp issues exist.
 |
Unbonded Screed |
An unbonded screed fails by lifting or curling, which is likely to happen when the screed is thin. Hence, the thickness of the unbonded screed is designed greater than 70 mm.
Advantages of Unbonded Screed
- Flooring is not in contact with the main substrate and thus remains unaffected by any deformations of the screed.
- Thick screeds can be provided without worrying about drying time or the formation of cracks similar to thinner sub-layers
- The PVC or polythene membrane provided sufficient damp proofing to prevent moisture-raising issues from the substrate.
3. Floating Screed
Floating screeds are a type of unbonded screed that is laid over an insulation layer or an underfloor heating system. The intermediate layer can be polystyrene or polyurethane panels or soundproofing material.
 |
Floating Screed |
The main objective of a floating screed is to provide solutions to meet the minimum performance requirements of soundproofing systems in buildings as per the local set laws.
The minimum thickness of a floating screed is calculated based on the intrinsic characteristics of the material used and the material stresses expected to come over the surface. A thickness of 65mm or greater is applied for heavy-loaded floors.
4. Heated Screed
A heated screed is a floating screed with elements embedded in the screed in spiral or coil pattern. These elements can be pipe-work in plastic or composite material with a metallic core.
 |
Heated Screed |
The thickness of the screed above the elements must be maintained at least 25 mm with a metallic mesh inserted in the screed as shown in the figure. The size of the mesh is dependent on the total thickness and the design loads.
The heated screed is laid only after checking the pipes for leaks and any other issues.
Miscellaneous Types of Screed
Screed can be created in a bonded, unbonded, or floating manner, depending on the specific construction needs. Within these methods, it can be reinforced or enhanced for increased wear resistance according to specific specifications. Additionally, screed is available in different types based on the chosen materials, which will be elaborated on in the forthcoming article.