Modular construction is the construction of building structures using modular units that are manufactured at a factory away from the real site. The modular units are transported from the factory to the site and assembled sequentially, to obtain the final structure.
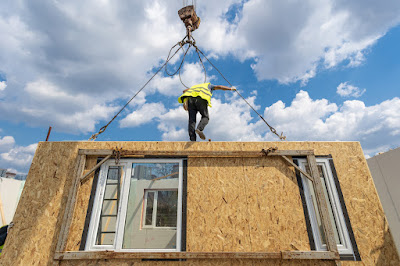 |
Image Credits: DBS Group |
Modular construction is a modern method of construction (MMC) technology that provides a proven solution for the increasing demand for social housing. Furthermore, it is also making headway in institutional construction by offering temporary classrooms that create exceptional learning spaces for growing minds in the form of modular classrooms.
To ensure the highest quality in modular construction projects, it is essential to meet the required standards at the construction site. Before installing module units, proper and sustainable site preparation is necessary. This involves engaging reputable services such as effective erosion control, dust suppression, and comprehensive rehabilitation if the site is not initially suitable. For instance,
environment services in South Australia have expert professionals who specialize in helping construction projects meet the region's high environmental standards.
This article encompasses the important pros and expected costs while performing modular construction.
Pros of Modular Construction
1. Cost-Effective
Modular construction employs modular units manufactured at a standard scale in similar numbers. Hence, they bring economy by not requiring formwork, scaffolding, casting, and related tedious processes. Therefore, compared to the conventional construction process, modular construction is cheap.
2. Fast
The process involves assembling and fixing the modular units at the site. They are performed with special officers and personnel.
3. Less Delay
Conventional construction is affected by weather conditions. Modular construction enables modular units to be fabricated in standard conditions following strict quality standards. Hence, there is no chance of delay in projects.
4. Flexible
Every modular construction project can be renovated from scratch. Except for the foundation, all other modular layouts can be changed to the new design and plans.
5. Superior Acoustics and Better Interiors
Prefabricated modules unlike traditional construction elements come with unique acoustic features and they become more flexible with the interiors.
6. Modular Construction is Environmentally Friendly
Modules are pre-planned and pre-built. All the required elements are on the site for assembly. Hence, modular construction is often considered an environmentally friendly construction method since it requires fewer materials, generates less waste, and results in a lower carbon footprint compared to traditional construction methods.
Additionally, modular buildings can be designed to be energy-efficient, with features such as efficient insulation, solar panels, and LED lighting.
7. Offers Consistent Quality
Since modular units are constructed in a factory-controlled environment, quality control is more consistent and thorough compared to on-site construction. This can result in higher-quality finished products with fewer defects, which can ultimately save time and money during the construction process.
8. Versatile
Modular construction is not limited to only housing and classroom applications. Modular units can be used for a variety of construction needs, including retail space, office buildings, medical facilities, and more.
9. Offers Faster Occupancy
Since modular construction is performed in a controlled environment, construction time is often shorter compared to on-site construction. This can result in faster occupancy and a quicker return on investment for investors.
10. Offers Cost Savings
Modular construction is often less expensive compared to traditional construction methods. Since the modules are prefabricated in a factory, there is less waste and labor required on-site, which can ultimately result in cost savings for investors.
11. Safer
Considering the safety of workers, modular construction just demands the placing of modules. It does not demand high-risk operations of workers like working at heights. Modular construction hence reduces the risk of injuries and is hence safer.
Cons of Modular Construction
The major cons of modular construction are:
1. Transportation
While modular construction can be more cost effective than traditional construction methods, it requires careful planning for transportation. Large modular units need to be transported from the factory to the construction site, which can be challenging in some locations. For example, if the site is located in a congested urban area or has limited access, it may be difficult to transport the units without causing disruption to traffic or the local community.
2. Module size
While modular construction can offer flexibility in terms of design, there are limitations to the size of the individual modules that can be manufactured and transported. In some cases, clients may need larger spaces than can be accommodated by modular units, which can make modular construction less suitable for certain types of projects. However, modular construction can be an ideal solution for projects that require repetitive units or structures, such as hotels, student housing, or hospitals.
3. Site requirements
Modular construction requires a regular and rectangular construction site that can accommodate the size and shape of the modular units. While this may not be an issue for many projects, it can be a limitation for projects with irregular or complex site conditions. However, modular construction can be adapted to different site conditions through careful planning and design. In addition to these, certain local authorities limit modular construction, as its standardization is not performed in every country.
Examples of Modular Construction
There are many examples of successful modular construction projects around the world. For example, in the UK, the YMCA opened a modular housing project in Brighton that provides affordable housing for young people. In the US, Marriott has used modular construction to build hotels in several locations, including New York City and California. In India, the government is promoting modular construction as a way to meet the growing demand for affordable housing. These examples demonstrate the potential of modular construction to deliver cost-effective, high-quality buildings in a variety of contexts.
0 Comments
Commenting Spam Links Are Against Policies